Off-site construction
Last updated: 9 August 2023
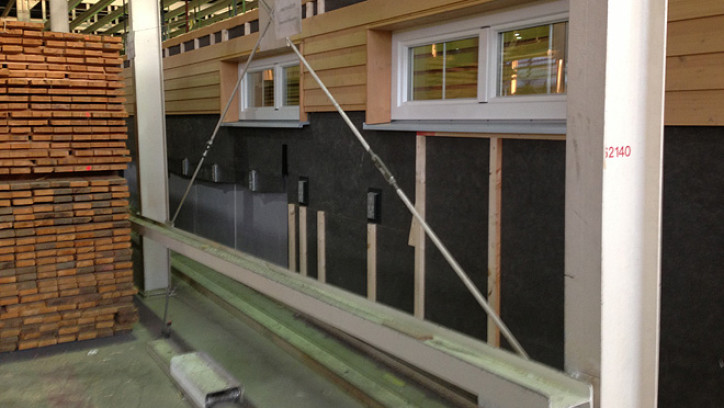
Off-site construction can help get your new home built faster.
Building off-site
Off-site construction has been part of New Zealand's construction scene in differing forms for decades. Examples include pre-nailed wall frames (componentised), kitset cottages (panelised), and transportable homes (modular). Some projects will use a combination of different types (hybrid).
Off-site construction has a number of potential advantages over on-site construction, including speed, weather protection, quality assurance, and waste management. However, whether these advantages exist depends heavily on the process and facilities of the prefabricators.
Off-site construction varies from relatively traditional construction in an open yard through to a highly automated process in a large factory – and everything in between.
In general, the more complete a home is when it leaves the factory; the less time is required onsite to finish it.
When to consider off-site construction
The use of panelised or modular prefabrication is decided at the very start of the design process. This is so designers can work with the factory and other building professionals to design the house in a way which is buildable, robust and transportable. Off-site construction companies will often have a list of designers who are accustomed to designing in a way that works for the company's facilities and processes.
Finance
Finance can be more difficult to sort out for some types of off-site construction. Most lenders finance new builds based on the staging and procurement patterns from traditional onsite construction. Off-site construction differs for a number of reasons:
- Work occurs over a much shorter timeframe.
- Site works and house construction often happen in tandem.
- Materials are possessed by the factory until such a time as the house is delivered to site.
In recent years a number of lenders have been working to make lending more compatible with off-site construction. Many companies offering off-site construction also offer build finance.
Consents and inspections
For off-site construction, the manufacturer or supplier is responsible for providing clear evidence of compliance with the New Zealand Building Code to the relevant building consent authority (BCA), as required by the Building Act.
It is possible to have your home built in a different place to where it will eventually be sited – this will involve two BCAs. The site's BCA will inspect the site works and foundations, and the connection of the home to the foundations and services, and any finishing work that takes place on-site. The factory’s BCA will inspect the house in various stages at the factory before it is transported.
How to support your building consent application has more information on the consent inspection process for off-site construction and building products certification.
Types of off-site construction
Componentised construction
Construction using prefabricated components is common in New Zealand – most building sites use multiple prefabricated items.
Componentisation is the most basic form of prefabrication. Components combine a number of items together make construction easier, faster, higher quality and/or more accurate into pieces that are ready to assemble or already assembled. This includes items such as pre-nailed roof trusses and wall framing, through to prefabricated, predrilled structural steel members.
Panelised construction
Panelised construction consists of sections of floors, walls, and/or roofs. These are built in sections to the drawings in the factory, delivered to the site, and then put together using special connections.
Panelised construction suits most sites where there is room for panels to be lifted or carried into place. Panelised construction often involves framed construction due to its lightweight nature, however it can also come in engineered or composite timber panels (eg cross-laminated timber or strand board), Structural Insulated Panels (SIPs), or precast concrete or concrete sandwich panels.
Modular construction
The most complete form of construction, modular construction requires good access to the site for module(s) to be craned into place. Where more than one module is used, these are connected once in place and made weathertight.
Modules can also be smaller in scale, such as internal modules containing complete kitchens, laundries and/or bathrooms – these are often used for large hotels and apartments. Once craned into place, the modules are connected to waiting services.
Generally, the maximum size of one module is less than 8m wide and 19m long, although the width and length of floor plans will vary depending on transportation rules and equipment. Typically, the stud height is kept to 2.4m due to height restrictions.
The size of the access (either at the site or on the way to the site) may limit the size of the module(s). In some cases, access may mean that panelised construction is a more viable option, for example low bridges or narrow roads on the way to the site, or a building site down a narrow driveway.
Transportable homes fall into the modular construction category.