Lap lengths for reinforcing steel mesh fabric
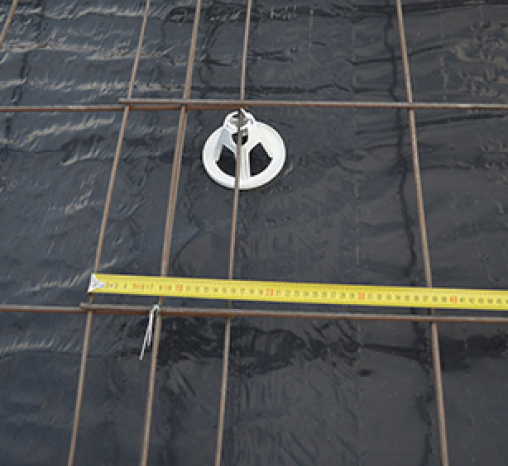
To ensure good performance, you need to make sure sheets of reinforcing steel mesh are properly lapped to prevent a crack from forming and the slab (or other concrete member) from failing, at the lap joints.
This information was confirmed as current in February 2016. It originally appeared in Codewords newsletters prior to January 2014.
Following the series of Canterbury earthquakes and the damage to concrete-slabs-on-ground, measures were introduced to the Building Code’s supporting document B1/AS1, to increase the resilience of concrete slabs on good ground against earthquake shaking.
One of these measures was the requirement for Grade 500E reinforcing mesh fabric, as explained in mesh for reinforcement of concrete slabs on ground.
Reinforcing steel mesh fabric is used (with and without other reinforcing steel) in concrete members such as floor slabs and walls. It resists forces and displacements induced by gravity loads, earthquake shaking, ground movement and shrinkage strains. Reinforcing steel mesh fabric is made from wires that are welded together to form sheets.
Laps need to be able to develop more than the elastic yield strength of the reinforcement, otherwise sudden failure can occur at the lap. This may be achieved either by following the Building Code supporting documents, or by an alternative solution proposal.
Building Code supporting document methods
All reinforcement must meet the requirements of steel reinforcing standard AS/NZS 4671:2001.
Verification Method B1/VM1
The Verification Method B1/VM1 cites the Concrete Structures (Design) Standard NZS 3101:2006 which provides two methods for determining the lap length. Both methods will produce a lap that is at least as strong as the characteristic elastic yield strength of the longitudinal wire that is being lapped.
Using two cross wires for anchorage: Clause 8.7.6(a) of NZS 3101:2006 requires a lap of one mesh space plus 50mm. The minimum is 150mm for plain round wire mesh. This relies on a cross wire weld developing in shear half the elastic yield strength of the largest mesh wire at the joint. This method may be used for both plain and deformed wire mesh. Our guidance on reinforcing mesh is based on this method.
Straight lapping of mesh wires: This method can only be used to lap deformed wire mesh. The Building and Housing Group’s guidance on reinforcing mesh specifies a lap length of 40 deformed wire diameters. A more optimal lap length may be calculated from NZS 3101. See Clause 8.7.6(b).
NZS 3101 does allow anchorage of plain round wire using hooks or bends (Clause 8.6.4) or mechanical anchorage (Clause 8.6.11). However, these methods are normally not practical or economic.
Acceptable Solution B1/AS1
This modifies NZS 3604:2011 by requiring a lap of 225mm, or the welded wire manufacturer’s requirements – whichever is greater.
Alternative solution proposal methods
Lap lengths can be varied from the above, if sufficient testing is carried out.
Testing must include lap length tests and cross bar weld strength tests, and must specify all the relevant test parameters, such as the minimum 28-day concrete compressive strength and wire mesh fabric properties (verified as meeting or exceeding AS/NZS 4671).
The assessment should also look at the potential impact on concrete crack formation at high stress levels. In other words, even if the lap length test performance is adequate, additional lap length allowance is still required, to limit crack formation resulting from the loss of reinforcement bond.
Such testing and assessment should be accompanied by a technical opinion from a building professional such as a chartered professional structural engineer.
For these Alternative Solutions, the information should be presented in such a way that building control officials can easily see how side and end laps are made, and that the basis for them is different from those laps specified in the Building Code supporting documents.